Como se hace una maquina de ordeñar
Los ordeños mecánicos están de moda, pues son una gran ventaja en cuanto a tiempo y recursos a la hora de ordeñar nuestras vacas.
En este articulo veremos como es el proceso de fabricación de una maquina u ordeño mecánico.
Los componentes de la máquina de ordeño se crean y ensamblan en varias plantas de fabricación importantes en todo el mundo utilizando procesos y procedimientos tradicionales. El acero inoxidable y el plástico se utilizan para contenedores y revestimientos, y en fundición y acero para bombas de vacío, controles y dispositivos de medición.
Recepción
Aquí el acero inoxidable se recibe en forma de lámina o tubo grande. El acero inoxidable se utiliza para fabricar componentes que entrarán en contacto con la leche. Las láminas están protegidas contra rasguños con un revestimiento de vinilo, que se eliminará más tarde después de la formación y el mecanizado.
En este punto, el acero inoxidable de la fundición tiene un acabado mate.
Corte, mecanizado y conformado.
Las hojas de acero pueden enviarse directamente a una estación de pulido donde las máquinas grandes crean un acabado suave.
Una vez que se logra el acabado inicial, las hojas pueden moverse sobre rodillos a máquinas punzonadoras controladas numéricamente , donde se cortan en formas para varias partes.
A partir de ahí, algunas partes se forman o doblan en forma en los frenos grandes. Los paneles de montaje para controles, componentes estructurales y piezas de pequeños detalles para las garras y bombas se fabrican en esta etapa.
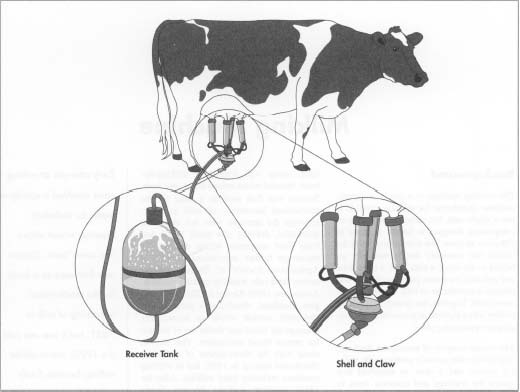
Creando la cáscara y las garras.
La cubierta que contiene el revestimiento se fabrica como una extrusión. Este proceso implica forzar la tubería de acero sobre una matriz bajo calor y presión para formar la pieza rígida alargada.
La garra se fabrica como una serie de piezas extrusionadas más pequeñas de tubos que forman el colector, que espacia las copas en una formación de racimo.
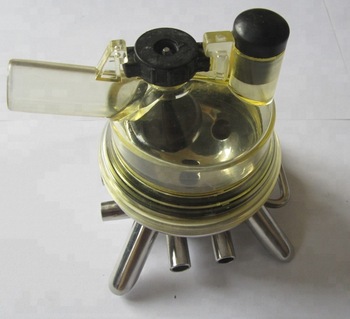
Luego, las extrusiones se sueldan manualmente en los accesorios de acuerdo con el tamaño deseado. Tanto las garras como la cáscara completadas tienen un acabado mate que requerirá pulido.
Haciendo los receptores
Los tanques de recepción son tanques de acero inoxidable que reciben leche de las líneas de leche, generalmente de 15-26 galones (60-100 1). Aunque algunos son de plástico personalizado, la mayoría son de acero con las cabezas o extremos girados en máquinas especiales. Esta técnica de producción da forma a un disco de acero delgado mientras se gira en un torno. El disco tiene forma, ya que está forzado sobre una forma de acero o mandril. Una vez que el operador forma los extremos del receptor en forma de tazas, otro técnico soldará el cuerpo a la cabeza, dejando orificios o aberturas para la entrada y salida de leche. Fabricados individualmente, los receptores también serán pulidos a mano. Algunos receptores tendrán inserciones de paneles de plástico translúcido para que los productores de leche puedan evaluar visualmente la producción de leche de vaca.
Pulido
Todos los componentes principales de acero inoxidable se pulen al acabado familiar asociado con el equipo de manejo de alimentos. Los fabricantes utilizan una variedad de correas, telas y ruedas giratorias mecanizadas en lo que se convierte en un proceso muy laborioso para cumplir con las normas sanitarias del gobierno y la industria. Este pulido es adicional al pulido que sufren las grandes láminas de acero inoxidable después de recibirlas. Los trabajadores manejan una variedad de pulidores de mano y accesorios para brillar todas las superficies de contacto y de protección, desde las garras hasta los receptores y las tuberías.
Haciendo las bombas de vacío o sopladores
Estos "controladores" de aire y fluidos a través del sistema son fabricados por proveedores seleccionados. La unidad es básicamente una caja de hierro sellada con un conjunto de engranajes de distribución en el interior y un impulsor, que se asemeja a dos cuchillas o paletas en un eje, que gira a más de 3.000 revoluciones por minuto para crear un vacío que dibujará fluidos en la línea.
La fabricación de las bombas requiere que se viertan piezas de fundición en bruto para las distintas partes. Las piezas en bruto se mecanizan a mano en un banco por técnicos y luego se colocan en una mesa de corte giratorio CNC donde la piedra de corte hace dos pases precisos a lo largo de los bordes predeterminados para cortar cualquier superficie en bruto.
El ensamblaje de los componentes principales, junto con los sellos, cojinetes y ejes, es crítico debido a una variación de solo 0. 002 pulgadas pueden cambiar el equilibrio y afectar a la bomba. Los componentes se colocan en una máquina de medición de coordenadas donde se verifica el perfil para que todas las piezas encajen correctamente. Los técnicos, utilizando medidores de palpación, establecerán los espacios adecuados antes de bloquear las piezas críticas del engranaje en su lugar y atornillar la unidad. Luego, harán funcionar las bombas en una cabina de prueba antes de liberarlas para su distribución.
Montaje
Las piezas fabricadas y compradas se colocan en varias áreas diferentes donde se juntan los subconjuntos de la máquina de ordeño. Los técnicos seleccionarán las piezas de acuerdo con las especificaciones de diseño del sistema, a menudo personalizadas para cumplir con ciertas operaciones. Es en esta etapa que las presiones y las cargas medirán el rendimiento del equipo. El ensamblaje final de todos los componentes de la máquina no se llevará a cabo hasta después del envío a la granja y la instalación en bams, donde a menudo se utilizarán puestos y estaciones elaborados para maximizar la cosecha de leche.
Los trabajadores en el ensamblaje también realizarán las conexiones de la línea inicial de válvulas a bombas y medidores, verificando las tolerancias y los ajustes inadecuados. Las bombas de vacío o los sopladores, el corazón del sistema de ordeño, se prueban para que tanto la leche como el aire que lo acompaña puedan eliminarse de manera eficiente. Las bombas serán probadas bajo cargas simuladas .
Se seleccionan los controladores de vacío, que admiten el aire necesario para mantener el nivel de vacío adecuado. Las líneas de aire y las líneas de leche se seleccionan por tamaño y hardware de conexión agrupados. Los controles, también comprados, están preparados para su instalación.
Si quieres conocer otros artículos parecidos a Como se hace una maquina de ordeñar puedes visitar la categoría GANADERIA.
Entradas relacionadas